FLATTENERS & DEWATERING
If you are in the waste or recycling business, paying to ship excess air and liquids will cut deeply into your profit margin. It is of utmost importance to find an efficient and cost-effective way to squeeze both out, maximizing the amount of desirable material in your payloads. Komar offers a wide range of equipment solutions to slash your transportation costs. Komar units provide proven compaction ratios of 4-7 times on containers and dewatering results of 50 to 85% depending upon the application.
Types
-
FLATTENERS
Container compactors for PET, HDPE, Aluminum Containers as well as Gable Top and TetraPak
-
DE-WATERERS
De-watering units for paper mills, municipal solid waste, and beverage containers
Flatteners
BOTTLE AND CAN FLATTENING 800-1500 lbs/hr
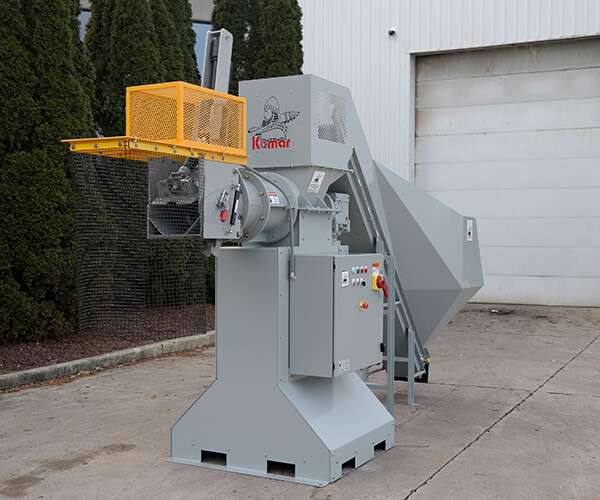
- Auger Type:
- Electromechanical, Stationary
- Facilities:
- Bottle and Can Deposit or Drop-Off Centers, Bottle and Can Baling Operations
- Application:
- Bottles, Cans, and Cartons
- Volume:
- Low
- Duty:
- Continuous
- Feed Methods:
- Hand, Conveyor
- Models:
- EPC-5, EPC-7.5
With only three major moving parts, the EPC product line redefines simple, reliable product compression. This technology compacts capped PET bottles with ease and HDPE, aluminum cans, and other recyclable containers. Utilizing clean all-electric drives, this series provides quiet, low maintenance operation.
- Compresses products 700%, slashing transportation costs
- Speeds downstream baling by over 50%
- Locates adjacent to buy back point to reduce site handling costs
- Improves downstream manual and automated sorting accuracy
- Low power consumption: can run on single or three-phase
- Fully prewired, ready to run.
- Ultra abrasion resistant metallurgy
- Can be configured as a standalone unit, a cartridge for insertion into a material recovery facility’s process line, or under a high-speed container sorting system
EPC 5 Specifications | |
weight | 2,100 lbs |
rpm | 43 |
hp | 5 |
base machine (l x w x h) | 16’7″ (maximum) x 46″ (maximum) x 8’6″ |
Compaction | PET: Adjustable 4-6 to 1 Aluminum: 3.5 to 1 |
Throughput/hr | PET: 700-1,000 lbs/hr Aluminum: Up to 800 lbs/hr |
Conveyor Load Height | 42″ |
Product Discharge Height | 60″ |
EPC 7.5 Specifications | |
weight | 2,100 lbs |
rpm | 63 |
hp | 7.5 |
base machine (l x w x h) | 16’7″ (maximum) x 46″ (maximum) x 8’6″ |
Compaction | PET: Adjustable 4-6 to 1 Aluminum: 3.5 to 1 |
Throughput/hr | PET: 1,000‐1,500 lbs/hr Aluminum: 1,300‐1,500 lbs/hr |
Conveyor Load Height | 42″ |
Product Discharge Height | 60″ |
HIGH CAPACITY BOTTLE AND CAN FLATTENING 8,000 lbs/hr
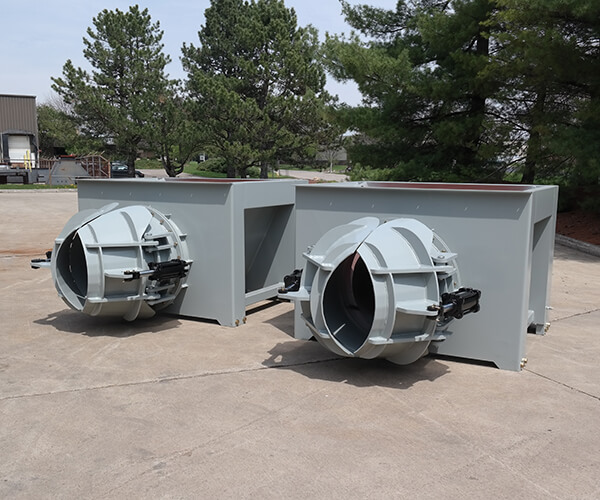
- Auger Type:
- Electromechanical, Stationary
- Facilities:
- Bottle and Can Recycling Facilities, Bottle and Can Producers
- Application:
- Bottles and Cans
- Volume:
- Medium
- Duty:
- Continuous
- Feed Methods:
- Conveyor, Tipper, Forklift
- Models:
- EPC-40
When you require very high throughput rates, it is time to consider Komar’s EPC-40. Designed for large-scale operations, the EPC-40 can process up to 8,000 lbs/hr at adjustable compaction rates of 4-8 times. The EPC-40 can handle capped bottles with ease and produces singulated, intact products for available optical sorting.
- Handles 8,000 lbs. of plastic per hour
- Adjustable compaction rates of 400%-800%
- Compact footprint inserts into existing process conveyor lines
- Can be mounted on a stand to rear load transfer trailers up to 40,000 lbs.
- Speeds downstream baling by 50%,
- Reduces bale wire use by 30%, improves bale weights by up to 20%
- Durable, clean, low maintenance operation
- Dewatering option for high volume product destruction
EPC 40 Specifications | |
weight | 10,300 lbs |
rpm | 20 |
hp | 40 |
base machine (l x w x h) | 11’5″ x 9′ x 4’8″ |
Compaction | 4 to 6 to 1 – Adjustable |
PET Throughput/hr | 8,000 lbs/hr. |
Larger 60hp units are available to 12,000 lbs/hr
MOBILE CONTAINER COMPACTION and TRANSPORTATION
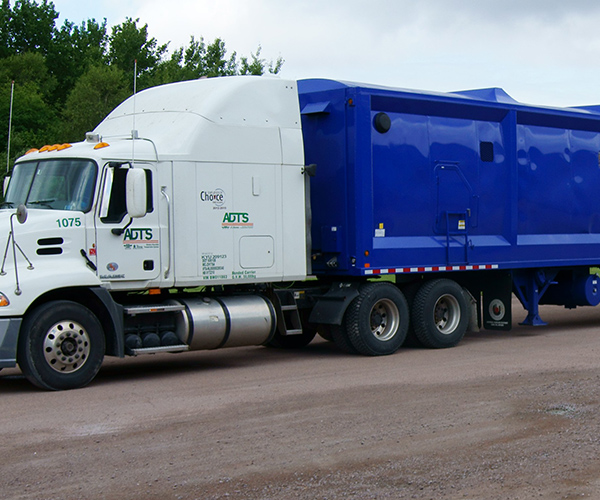
- Auger Type:
- HydroMechanical, Portable
- Facilities:
- Bottle and Can Deposit Recycling Centers
- Application:
- Bottle and Cans
- Volume:
- High
- Duty:
- Continuous
- Feed Methods:
- Integrated Rear Tipper
- Models:
- EPC-150
The current collection method of servicing depot systems in North America, collecting un-compacted bags of deposit containers in dry vans, is time-consuming and expensive. High-cost operations are due to labor-intensive loading and stacking operations, the necessity to ship back empty bags, and the resultant light payloads transported to processors. The EPC-150 compaction trailer rewrites PET collection rules by loading up to 4 tote bags per minute and carrying up to 30,000 lbs. of compacted aluminum cans or plastic bottles.
- Rapid rear tipping system tips 2 bags per cycle, handling 4 yds per minute.
- Loads, compacts, and compresses containers into trailer body in a single operation
- Carries up to 30,000 lbs of compacted containers
- Eliminates the need for small collection vans, and tote bag handling at collection centers
- Reduces offloading time to 10 minutes, eliminating all site labor
- Speeds up baling by 60%, can also deliver compacted material directly to the end processor.
- The trailer package includes soundproofed engine compartment with an exhaust silencer.
- Optional equipment includes an auto weigh system, GPS location tracking, EWON report support, and automatic maintenance reminders.
EPC 150 Specifications | |
engine type | diesel |
payload weight | Up to 30,000 lbs depending upon local GVWR |
hp | 150 |
base machine (l x w x h) | 53′ x 13’6″ x 8’5″ |
Compaction | 4 to 1 for Aluminum Cans, 6-10 to 1 for PET Containers |
PET Throughput/hr | Up to 12,000 lbs/hr (4 cubic yards per minute) |
Dewaterers
PAPER AND MSW DEWATERING 20,000 lbs/hr
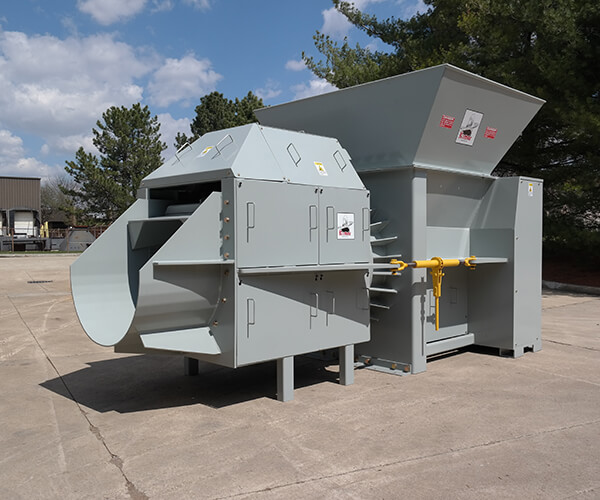
- Auger Type:
- Electromechanical, Stationary
- Facilities:
- Paper Mills, Industrial Depackaging, MSW and Organic Dewatering
- Application:
- Dewatering
- Volume:
- Medium
- Duty:
- Continuous
- Feed Methods:
- Forklift, Conveyor, Tipper
- Models:
- EM-40D (with dewatering unit)
Komar’s robust EM-40D auger, coupled with the proprietary maintenance-free wedge bar de-watering system, dramatically reduces hauling costs. This unique system leverages the EM-40D’s unrivaled 178,000 lbs. of thrust to create a compaction force that has demonstrated water removal rates of up to 85% from process reject streams. Proven applications include pulp mill rejects, industrial water jet fabric offcuts, organic separation residuals, and MSW dewatering.
- Reduces transport weights and landfill costs by up to 80%
- Feeds up to 15 wet tons per hour
- Self-cleaning wedge bar design minimizes blinding and ensures easy start-up.
- Handles oversized items and wire with ease
- An ideal choice for both batch and continuous operations
- An automated dewatering pressure gate applies consistent pressure for maximum results.
- The simplicity of design dramatically lowers lifecycle costs and allows for easily scheduled maintenance turnarounds.
- System paybacks of 1 to 2 years are common.
- Systems can be fed by forklift, tipper, or conveyor and can discharge into conveyors, compactors, roll-off boxes, or trailers.
EM-40D Specifications | |
weight | 17,750 lbs |
hp | 40 |
base machine (l x w x h) | 14’4″ x 8’3″ x 7’10” |
Free liquid removal | 80% to 90% depending upon application |
Throughput/hr | 15,000 to 30,000 lbs/hr depending upon feed method |
Available with optional hydrostatic drive system for high volume continuous operations.
CONTAINER DEWATERING
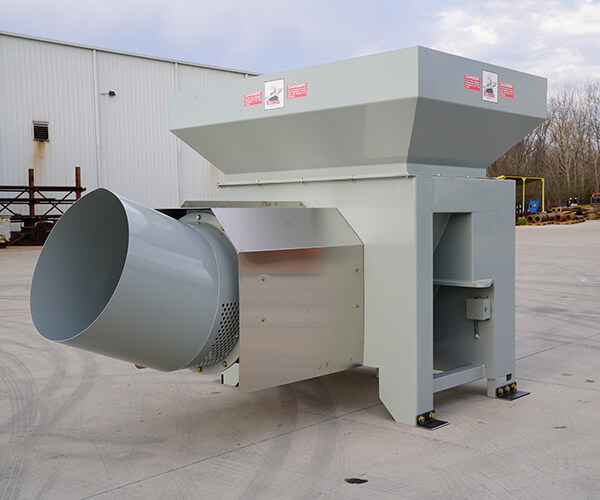
- Auger Type:
- Electromechanical, Stationary
- Facilities:
- Manufacturers, Organics Collection Companies
- Application:
- Dewatering, Bottles and Cans, Carton
- Volume:
- Medium
- Duty:
- Continuous
- Feed Methods:
- Forklift, Conveyor, Tipper
This solution is designed for an off-spec or expired product that still has value to other markets. This unit replaces traditional perforators with its unmatched ability to process an entire pallet of full containers per minute (equivalent to 216 gallons of liquid). As the auger screw ruptures the containers, the liquid drains through the holes in the processing chamber’s bottom and into a containment area.
- Processes 216 gallons per minute
- Perfect for the destruction of off-spec or expired product
- The liquid is collected and resold to secondary markets; dried containers are segregated and discharged for baling or transportation.