Which technology is best for fulfillment and distribution centers?
High-volume fulfillment centers and distribution warehouses generate a considerable amount of cardboard from their order fulfillment, re-packaging, and return processes. Depending on facility size, that amount of cardboard could be anywhere from 150 to 300 tons per month. This incredible volume of the material requires the most efficient, cost-effective, and reliable technology to process cardboard out of the facility. We believe that the Komar auger compactor (Komar Auger-Pak®) is the right solution for this objective, providing safety, no jams, and less labor.
The Myth of the Baled Premium
Depending on their geographical location, high-volume cardboard generating facilities can sell their cardboard to a recycler. When these facilities ask recyclers about the buyback rate for cardboard, many recyclers will indicate that they pay a $15 to $20 per ton premium for baled cardboard. Based on this buyback premium, a lot of generating facilities will decide to buy a baler.
As with all process equipment, there are costs associated with operating and maintaining a baler. When considering process efficiency, operational costs, maintenance and labor requirements, safety concerns, and reliability, it becomes evident that the small buyback premium recyclers pay for baled cardboard does not begin to cover the extra cost of producing bales.
The Komar Auger-Pak®
The Komar Auger-Pak® was invented to solve the issues with the traditional baling process. To understand how the auger eliminates these issues, it is essential first to understand how the Auger-Pak® works. Here is a step-by-step illustrated guide:
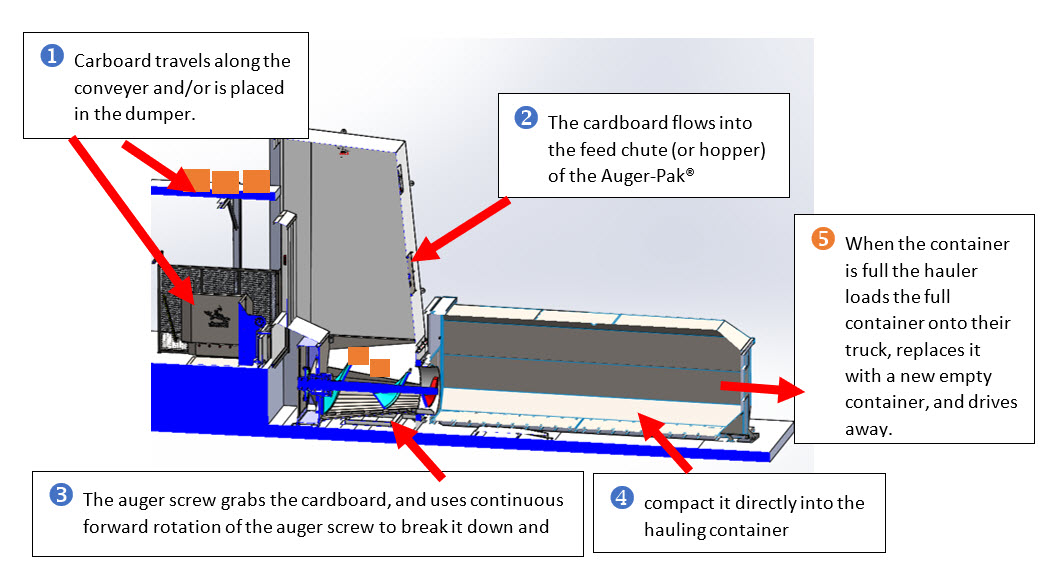
Benefits of the Komar Auger-Pak®
Regained Floor Space
The auger compactor sits outside of your facility.
Only the conveyor, or in some cases, the dumper, remains inside. Exposure to the elements is not a problem for the Auger-Pak® because it does not have intricate or fragile parts like those found in the baler’s auto-tie system. You will regain all of the floor space for the baler’s footprint, the dedicated forklift paths around the baler, and the area where you use to store the bales.
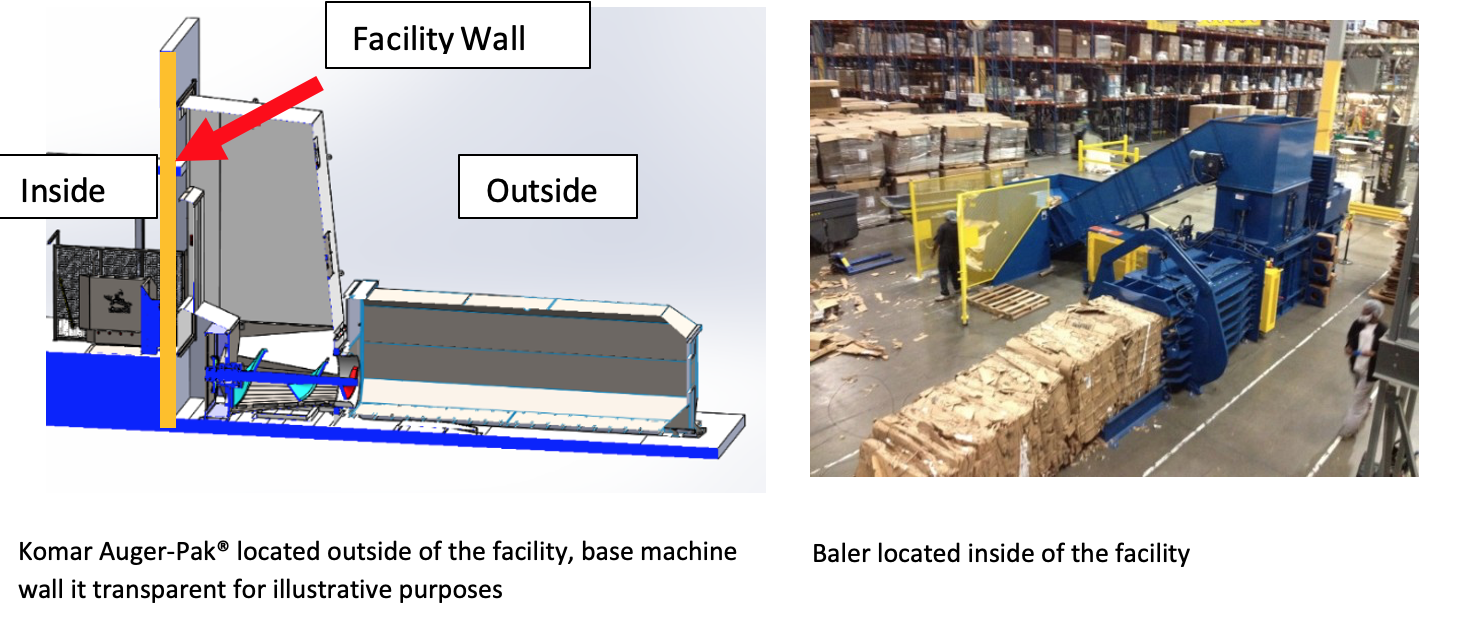
No Moving, Stacking and Loading Bales
The auger compactor packs directly into the hauling container.
Because the Auger-Pak® compacts cardboard directly into the hauling container, it eliminates the forklift and forklift operator’s need to handle bales. In addition to saving these resources’ direct cost, you also eliminate the associated maintenance costs for the forklift and the risk to your employees in moving and stacking heavy bales. When the hauler arrives, they do not have to wait for your employee to load their trailer. The roll-off container they pick up is already full and ready to be rolled off their flatbed.
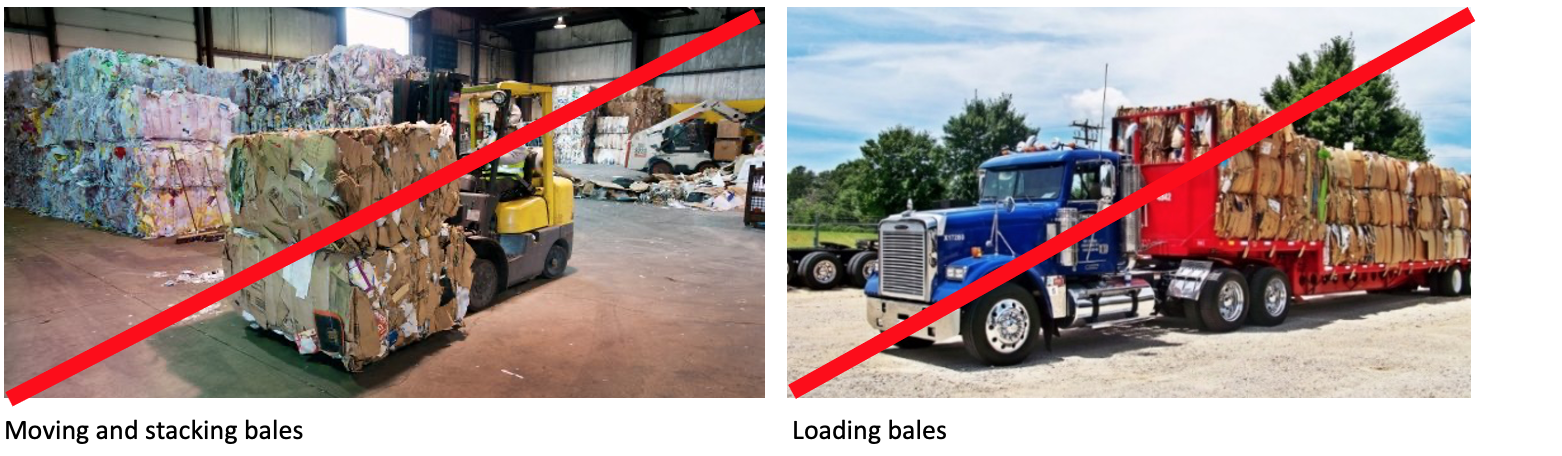
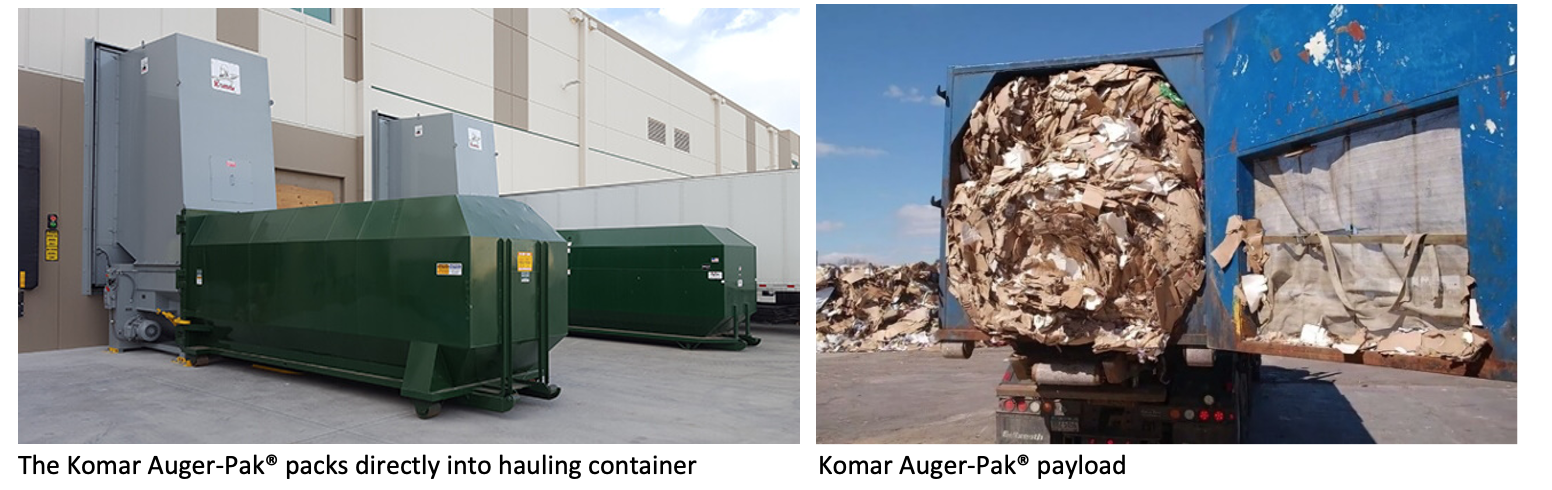
No Chute Jams
The auger’s in-feed is never blocked and is twice the size of a baler’s infeed, preventing chute jams.
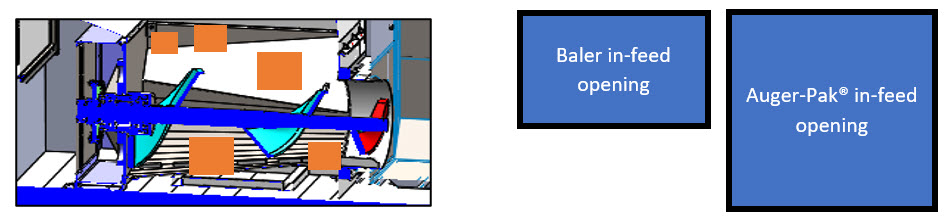
While a baler’s ram is compacting, it temporarily blocks the baler’s throat. During this time, cardboard backs up in the throat and is subject to jam. The relatively smaller size of the baller’s in-feed opening exacerbates this problem.
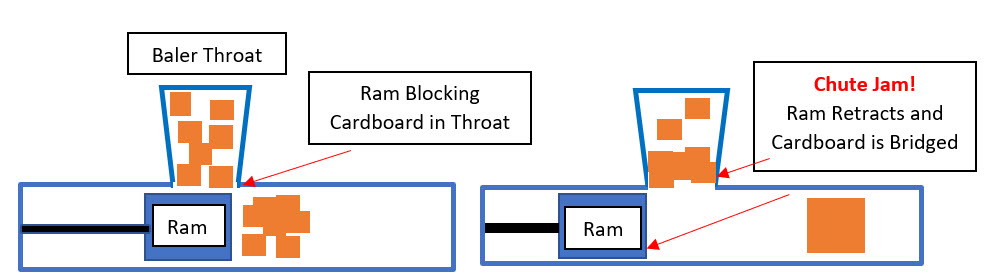
No Drag-Back
The auger does not experience drag-back because it always pushes material forward, eliminating spaces for material to become trapped. When a baler’s ram is retracting, it can catch some material just pushed forward and drag it back. Over time this material builds up under or behind the ram and causes jams that require downtime and labor to fix.
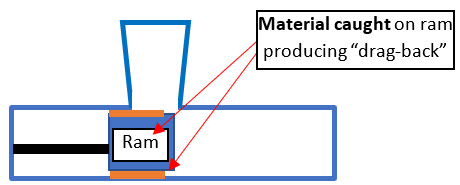
Simple Design for Lower Maintenance
The auger has one major moving part, the auger screw.
The Auger-Pak® utilizes the auger screw to break down the material and compacts it directly into the hauling container. Supported by a simple but strong self-lubricating bearing support system, the auger doesn’t have many tiny moving parts that can break down and cause processing disruption.
The baler’s auto-tie system is very complex.
The baler’s needle and threading of industrial-grade wire draw similarities to a loom or giant sewing machine. It has hundreds of tiny moving parts exposed continuously to debris that can stop them from working correctly. A full-time operator must be available to keep this system properly lubricated, aligned, and clear of debilitating debris. Due to the complexity and fragility of this process, the auto-tie system often malfunctions or breaks completely. This video shows an auto-tie system at work: an Auto-tie system at work.
Clean All-Electric Drive
Komar’s EM-Auger-Pak® line is all-electric. Electromechanical drives are inherently low maintenance and quiet, with no hydraulic oil leaks. Komar’s electric drives boast a 500% shock load rating to process difficult materials with ease. Hydraulic systems power a lot of industrial equipment, including some of Komar’s biggest auger compactors. However, if you do not need a hydraulic drive to do the job, an electromechanical drive is a simple, clean power option.
No Baling Wire
The wire to tie bales is expensive.
The average cost of wire per ton of baled cardboard is $5.33 to $5.88. The cost of wire alone takes away at least a fourth of the baled ton premium. Having wire under immense tension is a safety hazard. Whether it is loading a new role of heavy wire on the baler, adjusting the wire running down the baler, or fixing a problem inside the tying mechanism, these actions pose a serious risk of injury. Eliminating baler wire is much safer for your employees.
Eliminates Flammable Material Inside of Your Building
A Komar Auger-Pak® puts processed cardboard inside a hauling container’s metal enclosure, which has minimal access to oxygen. Installing an auger means a lower risk of fire, which will significantly drop insurance costs and the fire protection system’s cost. Cardboard is a very flammable material. Having a lot of cardboard stacked inside or outside of the facility is a safety risk. Because of this risk, the facility must upgrade its fire protection system when installing a baler.
Conclusion
When a recycler or a mill offers a $15-$20 per ton premium for baled cardboard, they are only offering the cardboard generating facility the amount of money the recycler/mill saves from having to bale it themselves. The recycler/mill wouldn’t offer more because they would lose money.
This reality implies that to make money at baling, the cardboard generating facility must have a more efficient baling operation than the recycler or the mill. Recyclers and mills bale cardboard as their primary business function. They have a completely optimized system with much bigger balers. The hydraulic technicians and mechanics on staff specialize in the baler’s systems and have an intricate understanding of how to drive cost out of the baling process.
In a fulfillment or distribution center, cardboard is a by-product of the primary business operations. The cost to bale cardboard will almost always be much higher than the $15-$20 per ton premium that the recycler/mill is paying to bale. The facility’s advantage is to have the most efficient and cost-effective way to get cardboard out of the facility. The Komar Auger-Pak® solves the problems and cost issues associated with baling, giving cardboard generating facilities a superior return on their investment.