Why Select An Auger Compactor?
You have decided that it is time for your company to replace an existing compactor or to purchase a new compactor for the first time. Suddenly, you are in a world of charge capacities, compaction ratios, crushing forces, and cycle times. It’s time to cut through the noise and focus on what’s really important: operational efficiency and a superior return on investment. This article is a high-level comparison between the ram compactor and the Komar auger compactor (Auger-Pak®).
Achieving Higher Compaction and Larger Payloads
The primary purpose of a compactor is to reduce material volume. The more material you can compact into the roll-off container, the more money you save on transportation costs. While both technologies promise high compaction ratios, it is essential to note that the Komar Auger-Pak® typically packs at least twice the volume into a roll-off container as the equivalent sized ram compactor.
Why is the Auger Better at Compacting?
Augers Shred & Compact in One Machine
Unlike a ram compactor, the Komar Auger-Pak® breaks up and shreds material as it compacts. The auger’s shredding capability is inherent to the continuous forward rotation of the auger screw. As the auger screw turns, it shreds. Enhanced by the tapered design of the processing chamber, this shredding action produces relatively small pieces as it pushes material into the roll-off container. We like to call this 3D destruction.
The ram compactor, on the other hand, only pushes material into the container. Because the material is not shredded, it does not compact as tightly. We call this 2D destruction. The 3D destruction of the Komar auger provides a higher compaction ratio, and as a result, a larger payload. Many of our customers have gone from one pull a day to one pull a week using the auger compactor.
Why is the Auger Faster and More Efficient?
Elimination of Cyclical Processing

This Processing Difference has Many Implications:
- No Cycle Time
The auger is faster because it does not spend half of its time going in reverse. - Continuous Feeding
The auger provides optimum processing with continuous metered feeding. Employees do not have to wait for a ram to reposition before putting more material into the processing chamber. - No Spring-Back
When a ram retracts, the material that was under pressure springs back. Spring-back causes loss of processing progress. The material must be re-compacted multiple times before it is small enough to be pushed into the roll-off container. An auger does not experience material spring-back.
Why is the Auger Lower Maintenance?
-
- All-Electric Drive
Hydraulic systems power a lot of industrial equipment, including some of Komar’s biggest auger compactors. However, if you do not need a hydraulic drive to do the job, an electromechanical drive is a simple, clean power option. Komar’s EM-Auger-Pak® line is all-electric and ranges from 15-180hp. Electromechanical drives are inherently low maintenance and quiet with no hydraulic oil leaks. Komar’s electric drives boast a 500% shock load rating to process difficult materials with ease. - No Drag-Back
When a ram is retracting, it can catch some material around the ram and drag it back. Over time this caught material builds up under and around the ram attracting unwanted pests. Periodic removal of the ram is required to clear away the debris. Drag-back can also cause jams that require downtime and labor to fix. The auger does not experience drag back because it is always pushing material forward, eliminating spaces for material to become trapped.
- All-Electric Drive
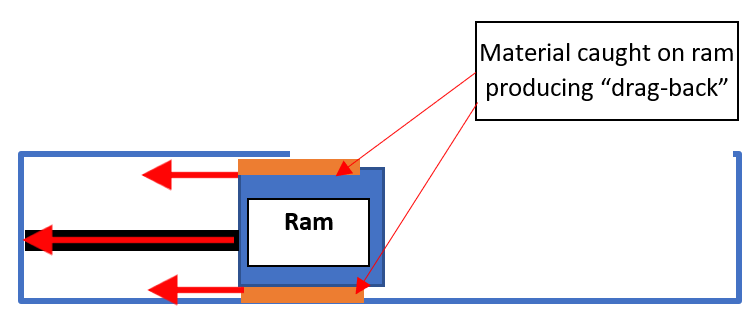
- No Chute Jamming
Chute jams occur when the flow of material builds up on top of the reciprocating ram during the retraction phase of the ram cycle. This build-up causes the material to jam or bridge across the chute opening. Often the compactor must be fully shut down to clear the jam manually, which is dangerous and labor-intensive.
Summary
When selecting a compactor it is important to focus on operational efficiency and a superior return on investment. The auger compactor’s method of processing, continuous forward rotation, prevents operational issues like spring-back, drag-back, and chute jamming. Eliminating these issues drastically cuts down on maintenance and labor costs. Continuous forward rotation also saves time, as the auger doesn’t have to reverse before compacting more material, nor is there additional wait time between loading. Finally, the auger utilizes 3-D destruction, shredding material as it compacts it into the roll-off container. Shredding leads to tighter compacting and, by extension, much larger payloads. Larger payloads mean a significant reduction in transportation costs. If you are ready to improve your operational efficiency and your bottom line, it’s time to consider an auger-compactor.