Komar Auger-Pak®
EM-General Series Compactors
- Shreds and compacts in one machine
- Substantially reduces transportation costs of general waste compactors
- Eliminates the need for a dangerous manual breakdown of general waste compactors
- Safely handles tramp metal such as nails and bolts
. – Bob Kagle, Director of Retail Logistics Goodwill SWPA
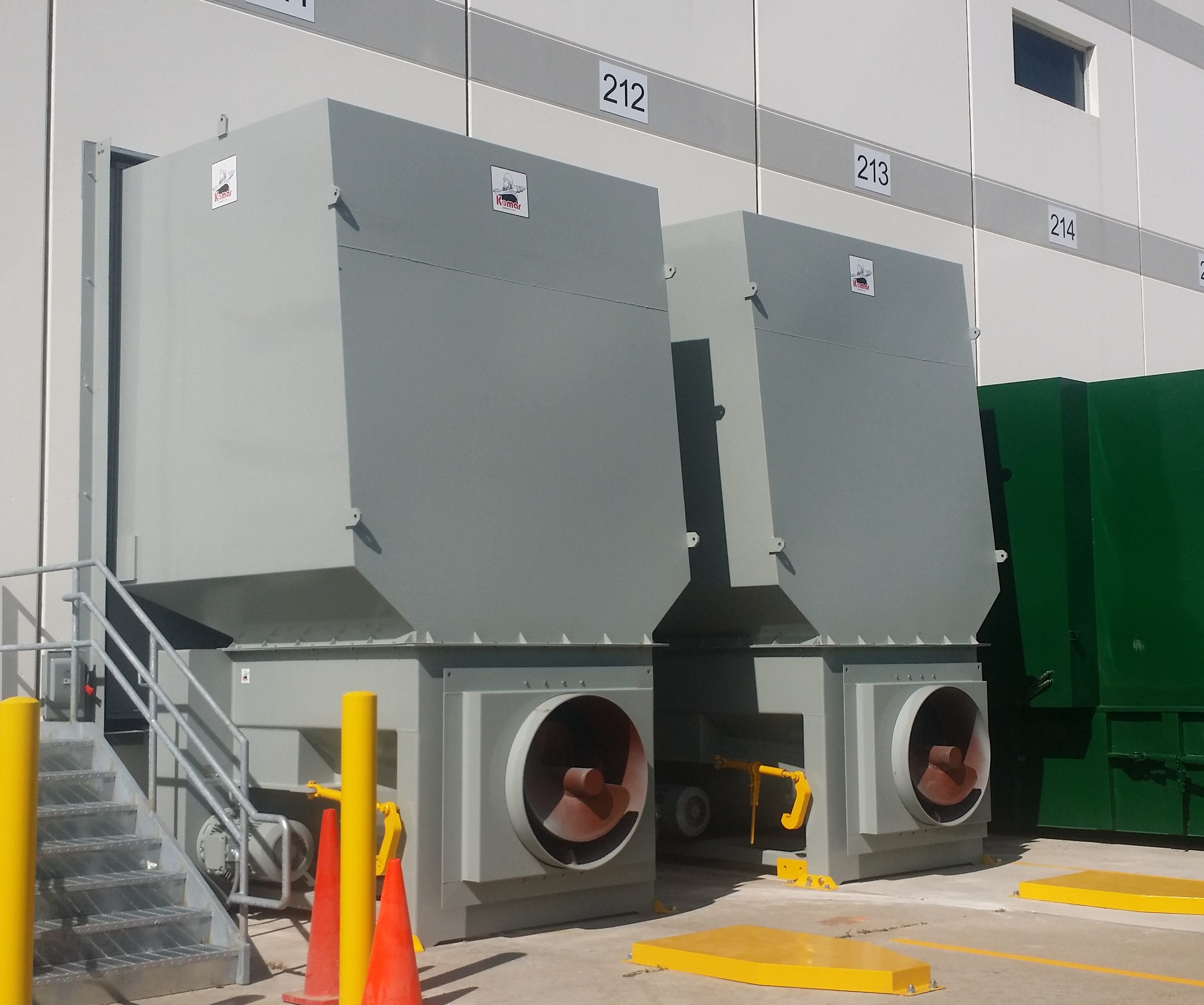

EM-15G
Processing Specifications | |
Horsepower | 15 |
General Waste | 2.76 tons/hr |
Cardboard | 1 ton/hr |
Feed Type | Hand, Forklift |
Receiving Container | Roll-off 40 cu. yd. |
Tons/Container | 4-8 (Depending on material and feed method*) |
Physical Specifications | |
Footprint (L x W x H) | 89.6″ x 72″ x 60″ |
Chamber Size (L x W) | 60″ x 59.25″ |
rpm | 7.42 |
torque (ft-lbs) | 10,624 |
Weight (lbs)** | 10,625 |
EM-20G
Processing Specifications | |
Horsepower | 20 |
General Waste | 4.9 tons/hr |
Cardboard | 2.5 tons/hr |
Furniture | 1.5 tons/hr |
Feed Type | Hand, Forklift, Tipper, Conveyor |
Receiving Container | Roll-off 40 cu. yd. |
Tons/Container | 4-8 (Depending on material and feed method*) |
Physical Specifications | |
Footprint (L x W x H) | 102.06″ x 83″ x 67″ |
Chamber Size (L x W) | 70″ x 69.5″ |
rpm | 5.97 |
torque (ft-lbs) | 17,602 |
Weight (lbs)** | 15,275 |
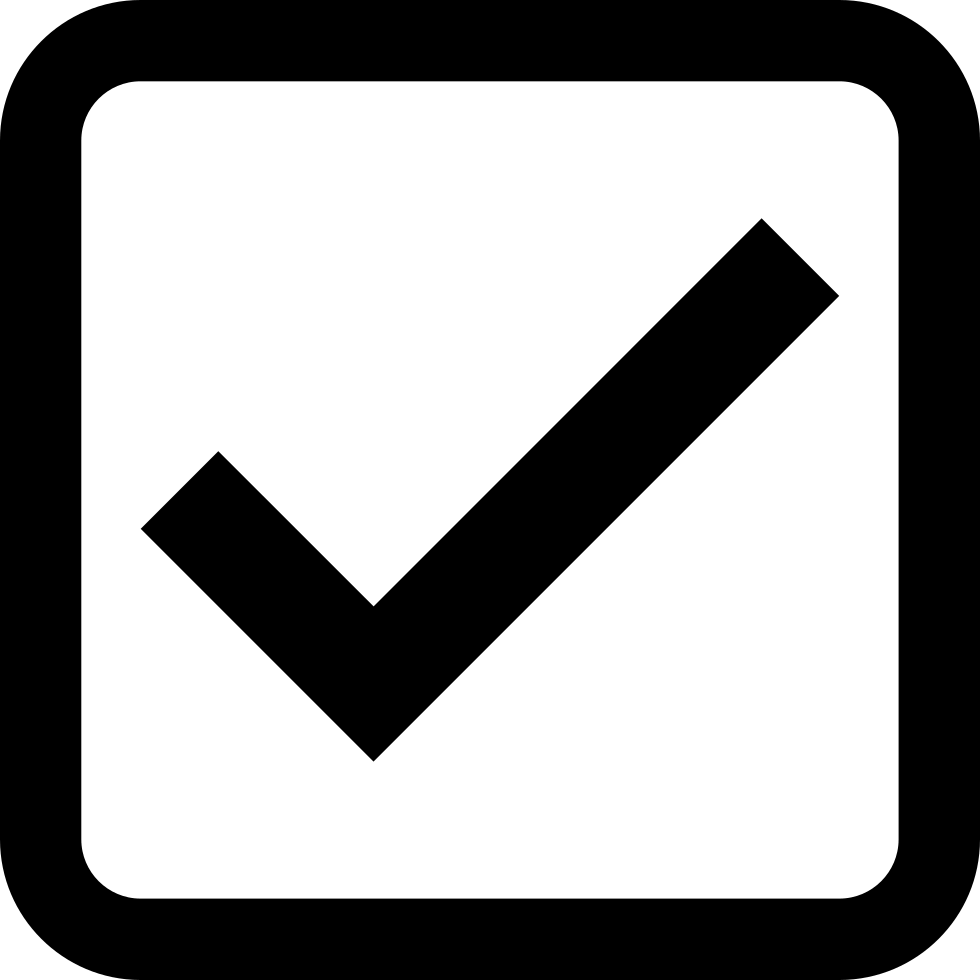
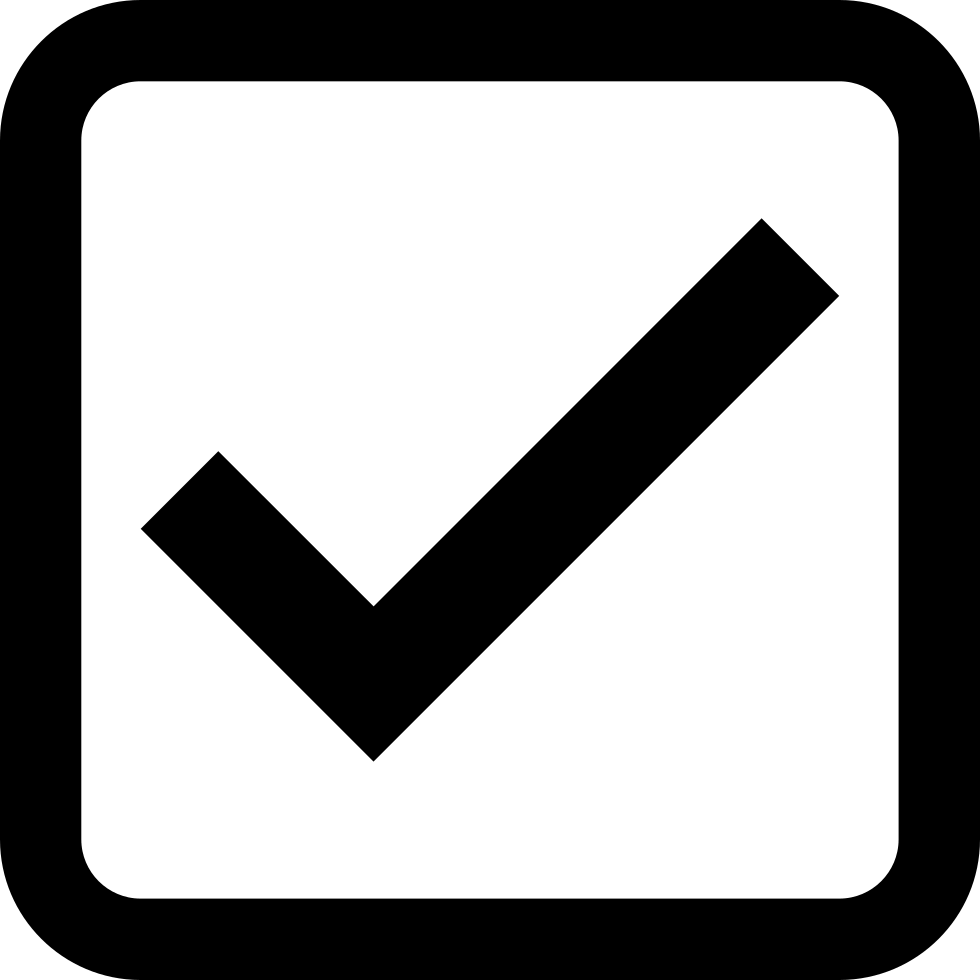
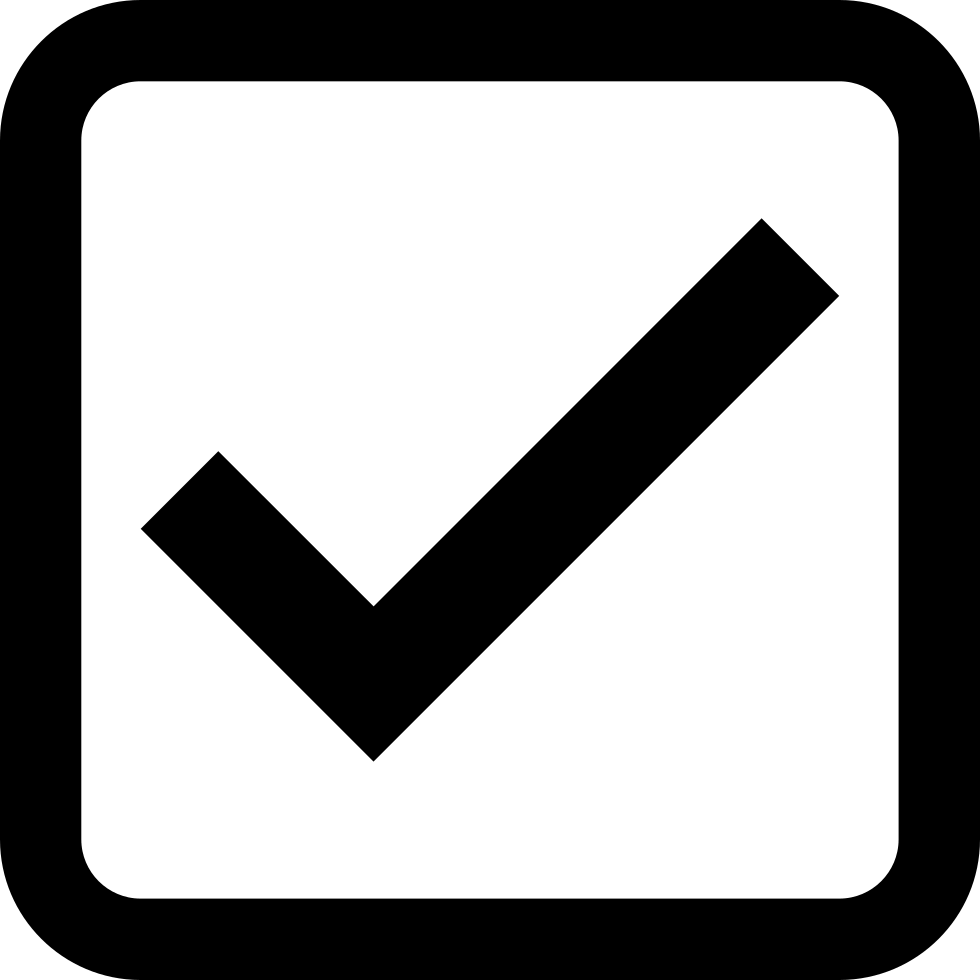
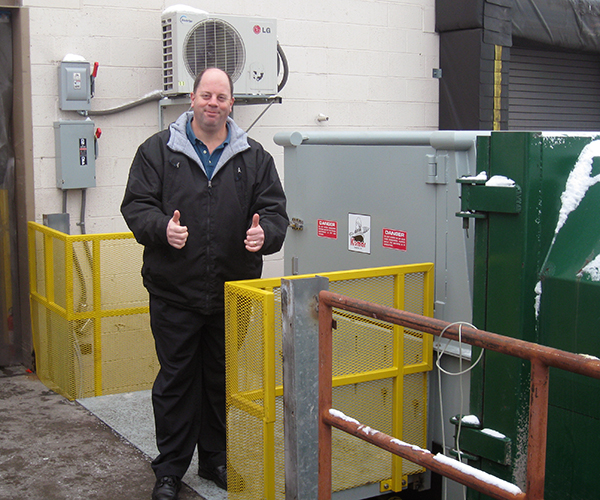
, which compacts 8.5 to 9 tons into each payload.” – Bob Kagle, Director of Retail Logistics
EMD-2020
Processing Specifications | |
Horsepower Drive 1 | 20 |
Horsepower Drive 2 | 20 |
General Waste | 1.8 tons/hr |
Feed Type | Hand, Tilt Truck, Tipper |
Receiving Container | Roll-off 40 cu. yd. |
Tons/Container | 4-8 (Depending on material and feed method*) |
Physical Specifications | |
Footprint (L x W x H) | 92″ x 96″ x 50″ |
Chamber Size (L x W) | 64″ x 84″ |
rpm | 9.47 |
torque (ft-lbs) | 520 psi per auger |
Weight (lbs)** | 14,933 |
EM-40G
Processing Specifications | |
Horsepower | 40 |
General Waste | 6 tons/hr |
Furniture | 3 tons/hr |
Feed Type | Hand, Forklift, Tipper, Conveyor |
Receiving Container | Roll-off 50 cu. yd. |
Tons/Container | 6-10 (Depending on material and feed method*) |
Physical Specifications | |
Footprint (L x W x H) | 115.75″ x 91.75″ x 68.5″ |
Chamber Size (L x W) | 80″ x 75.25″ |
rpm | 7.42 |
torque (ft-lbs) | 28,331 |
Weight (lbs)** | 19,085 |
EM-40GHS
Processing Specifications | |
Horsepower | 40 |
Cardboard | 5 tons/hr |
Feed Type | Hand, Forklift, Tipper, Conveyor, Chute |
Receiving Container | Roll-off 50 cu. yd. |
Tons/Container | 6-10 (Depending on material and feed method*) |
Physical Specifications | |
Footprint (L x W x H) | 115.75″ x 91.75″ x 68.5″ |
Chamber Size (L x W) | 80″ x 75.25″ |
rpm | 14.83 |
torque (ft-lbs) | 14,165 |
Weight (lbs)** | 18,825 |
EM-60G
Processing Specifications | |
Horsepower | 60 |
General Waste | 6.4 tons/hr |
Feed Type | Hand, Forklift, Tipper, Conveyor, Chute |
Receiving Container | Roll-off up to 75 cu. yd. or transfer trailer |
Tons/Container | Up to legal road limit |
Physical Specifications | |
Footprint (L x W x H) | 128.25″ x 92″ x 65.5″ |
Chamber Size (L x W) | 92″ x 75.25″ |
rpm | 10.17 |
torque (ft-lbs) | 30,972 |
Weight (lbs)** | 24,258 |
Series Technology
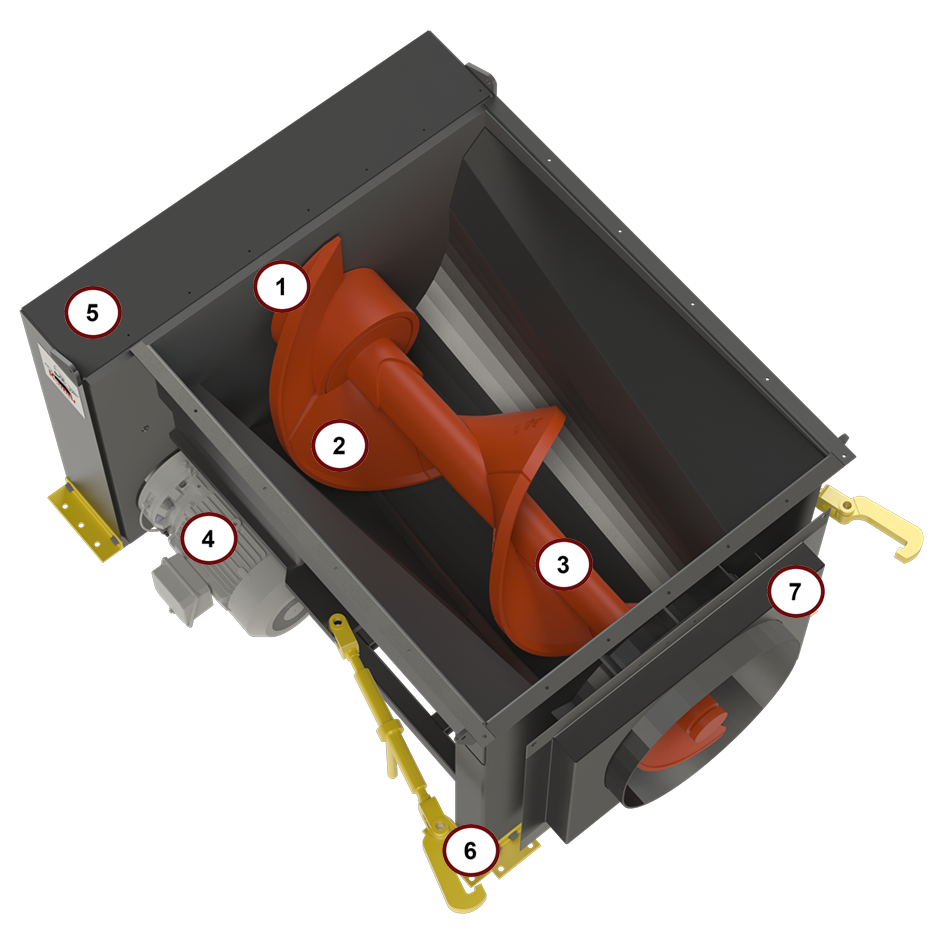
Patented Solid Lube Bearing Support System
Allows for the use of the biggest and most powerful auger screws in the industry, resulting in maximum compaction force.
Cast Steel Flights
Tapered Solid Alloy Steel Shaft
Using the highest quality components to construct our auger screws provides extended service life. The density and shape of the cast flights increase strength and durability and more efficient material delivery to the receiving container. Our patented tapered shaft uniquely distributes forces along the shaft, minimizing stress on the bearings and maximizes shaft life.
Cycloidal Drive with 500% Shock Load
Don’t judge a drive strictly by the motor’s horsepower, especially when you plan to process heavy industrial materials. A high shock load rating is vital in giving the compactor the ability to crunch through large loads without causing damage to the drive.
Worry-Free Chain and Bearing Lubrication System
The engineered, automatically lubricated chain, coupled with the self-lubricating bearing system, cuts down routine maintenance.
Ratchet Binders
Container Adaptor
The auger compacts directly into a standard roll-off receiving container typically provided by your local hauler and meet ANSI and OSHA specifications.
Compare our technology:
+ Auger-Pak® vs. Ram Compactor
1.) More efficient processing
2.) Fewer material jams
3.) Compacts two to four times tonnage into each receiving container.
4.) Half the power consumption
5.) Smaller footprint
6.) Easier to maintain
+ Auger-Pak® vs. Auto-Tie Baler
1.) More efficient processing
2.) Fewer material jams
3.) No auto-tie system. No baling wire to buy and store.
4.) Eliminates the double and triple material handling inherent in moving bales.
6.) Sits outside of the facility and compacts directly in the receiving container – no bales to store
7.) A lot of valuable floor space is given back to your primary business operations.
8.) It only requires one part-time operator to run and maintain.